What should the employer know when starting the construction project?
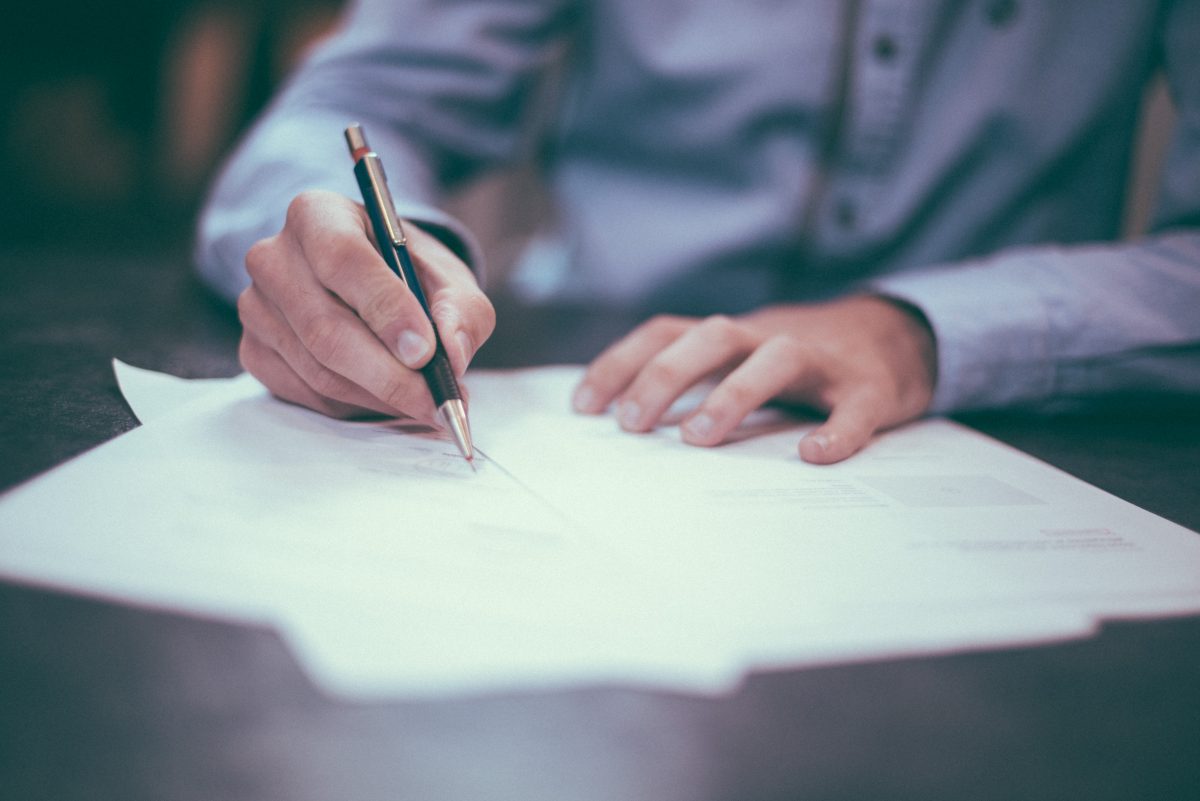
In Latvia, there are actually three different stories about construction – the public sector, the private sector, and a separate one from the private sector – private house construction, which, in the authors’ opinion, is poorly controlled and runs in a kind of self-sustaining flow. Professional experience has shown that the problems encountered by those involved in the construction process are quite varied and can be attributed to a number of factors.
The construction industry can introduce principles, methods and standards that will bring the industry as a whole closer to an efficient construction process and a wise use of resources (time and money).
In this article, we will look at a number of principles relating to the construction process that are most relevant for public procurers.
Golden Principles in Contracts
The Latvian Construction Council has agreed that FIDIC standard contracts will be applied in public procurements above EUR 5 million. It should be remembered that the method of construction project delivery chosen for each individual project will also provide the opportunity to choose the most appropriate FIDIC contract template, the general terms of which can be adapted to the specific situation. This is in order to avoid the situation often seen in practice where changes to the FIDIC Standard Contract effectively make it a “patchwork of rules”, thereby losing the fundamental principles embodied in FIDIC contracts. It would be useful to follow the FIDIC “Golden Principles” when carrying out this work.
The FIDIC Golden Principles are as follows:
- The duties, rights, obligations, roles and responsibilities of all the Contract Participants must be generally as implied in the General Conditions, and appropriate to the requirements of the project.
- The Particular Conditions must be drafted clearly and unambiguously.
- The Particular Conditions must not change the balance of risk/reward allocation provided for in the General Conditions.
- All time periods specified in the Contract for Contract Participants to perform their obligations must be of reasonable duration.
- Unless there is a conflict with the governing law of the Contract, all formal disputes must be referred to a Dispute Avoidance/Adjudication Board (or a Dispute Adjudication Board, if applicable) for a provisionally binding decision as a condition precedent to arbitration.
How to replace the lowest price while making the process efficient?
There has been a debate at various levels and in various forms, including in the European Parliament, on how and with whom to replace the lowest price principle. It is undeniable that this has primarily focused on the public sector and the public procurement system.
EFCA, as the representative organisation for FIDIC in Europe, has published material on the most economically advantageous tender (MEAT). EFCA’s methodology for achieving the correct MEAT criteria is based on a systematic five-step approach:
- Formulate main project goals.
- Derive possible quality criteria.
- Choose a maximum of 4 criteria.
- Attribute weights to the criteria.
- Test the set by performing a crash test.
When defining the objectives of a project, it is important to define their nature. There are two types of objectives:
- related to the product, the project;
- related to the project implementation process.
The project objectives may include various criteria, but the authors consider it important to define how and for how long the construction process will take place.
The second step is to obtain possible quality criteria. The range of criteria can be very wide in order to obtain the best tender. The most important thing is that the criteria are relevant to the project and its objectives. The following aspects should be taken into account when formulating the quality criteria:
- they must be linked to the contract;
- ensure non-discriminatory application without the possibility of arbitrary decisions;
- information on the partners submitting a tender must be verifiable;
- the selection guidelines must provide sufficient information to tenderers;
- the evaluation of quality criteria must be sound and effective;
- the possibility of a stepwise evaluation is needed to allow a real ranking of the quality of tenders instead of a yes/no mark for a requirement;
- the same aspects should not be used in the selection in a two-stage procurement procedure;
- the criteria impose costs on tenderers: the more and more complex the criteria, the higher the transaction costs;
- innovation is not a criterion in itself, but if it is wanted in a project, innovations should be assessed on the added value
- they bring to the project’s objectives.
The award criteria are developed differently depending on whether the contract focuses on consultancy or planning services. The eight different sectors in which criteria can be set are listed below:
- functionality;
- accessibility;
- aesthetics;
- sustainability of the product;
- process sustainability;
- life cycle costing;
- risk management, which includes feasibility studies;
- environment.
The quality criteria must be clearly described in the tender documents so that tenderers know what the requirements are and how they will be assessed and reviewed.
EFCA points out that care should be taken in the selection of criteria. Once the award criteria have been developed, their number should be limited, primarily for statistical reasons. The more criteria, the greater the dampening effect. The result will be that price, which is undeniably one of the award criteria, will have an increasing influence. The maximum number of criteria recommended is four, with price as the fifth criterion.
Money is an important reason for limiting the criteria. For applicants, meeting the criteria requires effort, time and therefore money. The more criteria, the higher the transaction costs. At this stage it is important to understand the chosen criteria and to discuss them with the contracted engineering consultant, as depending on the planned project, location and other criteria, a number of design and quality criteria may not be necessary. Any selection elements will always cost money, so it is important that the engineering consultant engaged has sufficient experience in the construction area in which the project will be carried out.
After selecting the four criteria, each of them should be given a relative weight. The first decision to be taken is the price/quality ratio. Many arguments can be put forward, but there is a general view that quality has a significant influence if price and quality are given equal weight. It is essentially a question of proportionality.
The final step is the so-called “crash” test, which can be carried out by asking the following questions:
- how big is the price difference between the lowest bidder and the highest bidder?
- how big is the financial difference if two bidders perform almost identically?
- how much are you willing to pay if the second bidder is of higher quality and the lowest bidder does not win?
This test can help you understand the impact of quality on costs and the project as a whole. If quality is too expensive to allocate, you can adjust the price/quality ratio accordingly.
Construction methods
It is important to understand the methods that will be used in the construction industry to deliver a construction project. Each method has its advantages and disadvantages. The choice of the construction delivery method is an important stage in project planning and certainly the choice of method needs to be considered in conjunction with the applicable contractual provisions, selection criteria, etc.
The project delivery method is the system of practical arrangements for organising, managing and financing the activities associated with the implementation of a project: pre-project stage, project design, procurement of works, construction works and operation and management of the structure. Each project delivery method has a different pattern of contractual relations between the actors involved in the construction process.
The main criteria for selecting a method are safety, cost, quality, time, site context and relevance to the intended objectives, as well as an assessment of all risks. Closely linked to the project delivery method are the procurement strategy, contract terms, payment methods and the architect’s form of project government and coordination.
The main construction methods are:
- Design – Bid – Build (BDB);
- Construction Management (CM);
- Design – Build (DB);
- Integrated Project Delivery (IPD).
Conclusion
The most important things to think about in this article are time and money. In particular, how are these resources managed in public (and not only) procurement, and are the professionals who have an employment relationship with the client always really professionals whose expertise is such that, whatever they are planning to build – a school or a bridge – they understand and know how to do it most efficiently? The answer to this question can be found in the statistics on the projects carried out by each individual client – how often the client has extended the time limit for construction (project implementation) and made additional payments in relation to the originally agreed procurement amount.